Preheating before welding and heat treatment after welding are crucial for ensuring welding quality. The welding of important components, alloy steel, and thick parts necessitates preheating before welding. The primary functions of preheating before welding are as follows:
(1) Preheating slows down the cooling rate after welding, facilitating the escape of diffuse hydrogen in the weld metal and avoiding hydrogen-induced cracks. Simultaneously, it reduces the hardening degree of the weld and heat-affected zone, improving the crack resistance of the welded joint.
(2) Preheating diminishes welding stress. Uniform local preheating or overall preheating reduces the temperature difference (also known as temperature gradient) between the workpieces to be welded in the welding area. This reduction in temperature difference not only decreases welding stress but also lowers the welding strain rate, helping to prevent welding cracks.
(3) Preheating decreases the constraint of the welded structure, especially in corner joints. As the preheating temperature increases, the incidence rate of cracks decreases.
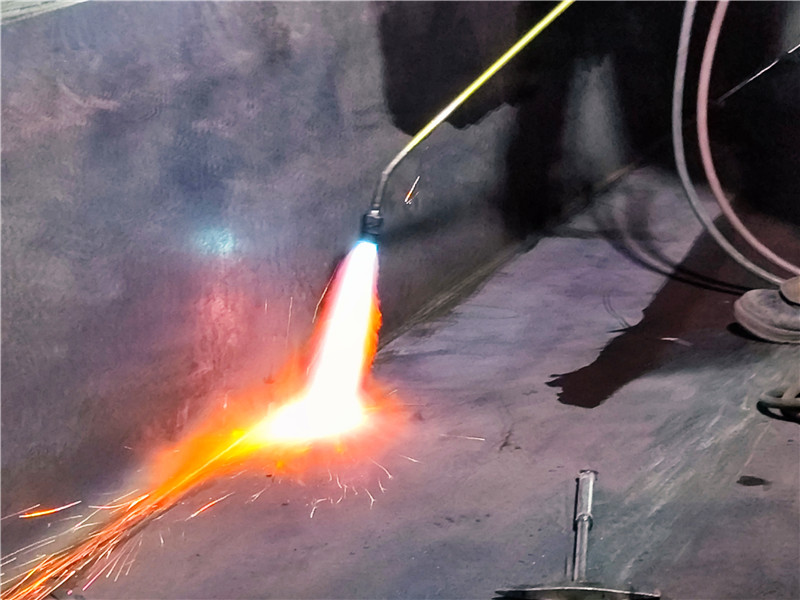
The selection of preheating temperature and interlayer temperature depends not only on the chemical composition of the steel and welding rod but also on the rigidity of the welding structure, welding method, ambient temperature, etc. A comprehensive consideration of these factors is essential for determining the appropriate temperatures. Additionally, the uniformity of preheating temperature in the thickness direction of the steel plate and the weld area significantly impacts the reduction of welding stress. The width of local preheating should be determined based on the restraint condition of the workpiece to be welded, generally being three times the wall thickness around the weld area, and should not be less than 150-200 mm. Uneven preheating, instead of reducing welding stress, can increase it.
Post-weld heat treatment
The purpose of post-weld heat treatment is threefold: eliminate hydrogen, relieve welding stress, and enhance the weld structure and overall performance.
Post-weld hydrogen elimination treatment refers to low-temperature heat treatment performed after welding is completed and the weld has not cooled below 100°C. The general specification is to heat to 200~350℃ and keep warm for 2-6 hours. The primary function is to expedite the escape of hydrogen in the weld and heat-affected zone, effectively preventing welding cracks in low-alloy steel welding.
During the welding process, welding stress is generated in the component due to uneven heating and cooling, as well as the constraints or external factors. The existence of welding stress reduces the actual load-bearing capacity of the welded joint area, causing plastic deformation and, in severe cases, damage to the component.
Stress relief heat treatment aims to reduce the yield strength of the welded workpiece under high temperature, relaxing welding stress. Two commonly used methods are overall high-temperature tempering and local high-temperature tempering. Overall high-temperature tempering involves placing the entire weldment into a heating furnace, slowly heating it to a certain temperature, keeping it warm for a period, and then cooling it in the air or furnace. This method can eliminate 80%-90% of welding stress. Local high-temperature tempering heats only the weld and its surrounding area, slowly cooling it to reduce the peak value of welding stress, making the stress distribution gentler and partially eliminating welding stress.
After welding some alloy steel materials, the welded joints may have hardened structures, deteriorating the mechanical properties of the materials. Moreover, this hardened structure may cause joint damage under the influence of welding stress and hydrogen. Heat treatment can improve the metallographic structure of the joint, enhancing the plasticity and toughness of the welded joint and, consequently, improving the comprehensive mechanical properties of the welded joint.